Future Textile Manufacturing – Use of recycled materials and support from new technologies
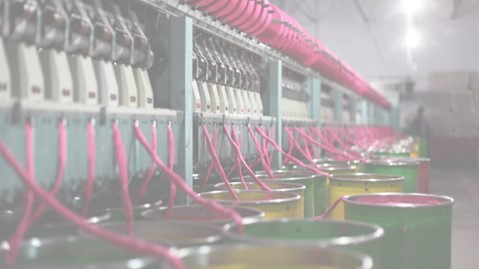
In textile manufacturing, the current manufacturing process is well suited for processing virgin fibers. This is because natural fibers, such as cotton, contain natural impurities that require harsh treatment. On the other hand, man-made fibers, like viscose and polyester, have fewer impurities and can be treated more gently. Furthermore, the length, strength, and elongation of virgin fibers are consistently uniform, making them easy to process. In contrast, mechanical recycled fibers vary in length, strength, and elongation due to their previous usage and lifespan. Consequently, producing high-quality products from recycled materials necessitates significant adjustments to the existing machinery. Although pre-treatment (i.e., collecting, sorting, shredding) is challenging due to the inadequacy of current equipment and processes for high-volume production. Implementing a distinct collection option could potentially resolve this problem, however it would involve significant logistical challenges. Sorting is a crucial requirement for recycling; however, the development of high-speed automated sorting devices is still ongoing.
For this study, we conducted a comprehensive literature review on the modifications made by textile machinery manufacturers and their impact on the production of recycled materials. Additionally, we conducted a survey to determine the specific focus on artificial intelligence, robotics, smart technology, and automation in the textile industry. Below is a summary of the literature’s findings.
Adjustment of current processes and processing lines
Siptex is an innovative facility that utilizes near-infrared light to efficiently categorize textiles based on their color and fiber composition. This technology allows for the efficient management of substantial volumes and generates textile fractions that are suitable for a range of recycling methods. The plant is capable of sorting three different flows at the same time with the capacity of 4.5 tonnes per hour. The plant manages textile waste from various sources, including consumers, pre-consumers, and industry. Meanwhile, VTT is extensively working on the NIR based sorting and has achieved the following fraction and it could be future significant for the textile sorting industries.
- 100% Cotton (CO), 100% Polyester (PES) and 100% Viscose (CV).
- Cotton/Polyester CO/PES and Cotton/Elastane (CO/EL)
- Wool/Cashmere (WO/WS) and Wool/Polyamide/Elastane (WO/PA/EL), or coated fabrics or fabrics with functional finishes
Andritz has pioneered a system that allows for the efficient treatment of both pre- and post-consumer textile waste. This waste includes natural and synthetic materials commonly found in apparel, linens, carpets, and technical textiles. In summary, this technique efficiently processes and produces a refined textile product by eliminating bulky and metallic components, such as bale wire, buttons, zippers, rivets, ornaments, and other impurities.
Rieter’s ring spinning technology for recycled fibers produces stronger yarns than rotor spinning. This technology helps weavers and knitters make fine, compact yarns with approximately 40% recycled fibers and excellent quality. The comber removes short fibers and neps from recycled and virgin cotton blends, increasing recycled content and quality. Running behavior, hairiness, and tenacity of yarn are improved by the COMPACTdrum device on the ring spinning machine. Short-fiber applications are the focus of Rieter’s rotor spinning technology. High yarn toughness and excellent piecing are smoothly combined by the fully automated machine. Using 80% post-consumer and 20% recycled polyester, Ne 20 yarn can be spun. Rieter claims their ring spinning can create Ne 6 to Ne 30, 100% cotton yarn with 30% recycled cotton, blends with man-made fibers with 50% recycled cotton. Compact Spinning may produce 100% cotton yarn with up to 40% recycled cotton. Rotor recycling system, Ne 3 to Ne 25 100% cotton yarn with up to 50% recycled cotton, blends with man-made fibers with up to 70% recycled cotton (finer yarn counts possible). Meanwhile, Trutzschler develops the pretreatment with the tearing lines, modified licker-in for the better process of recycled materials, introducing the 10 chambers for the better homogeneity of recycled and virgin fibers. Apart from that they introduced a digital solution which enables monitoring process, condition of wire clothings makes the process easy.
Andritz offers a range of recycled fiber products, including airlay (upto 100 % recycled fibers), needle punching (upto 100 % recycled fibers), spanlace (upto 65 % recycled fibers), and wetlaid CP (carded-pump; upto 25 % recycled fibers), suitable for various applications like building, construction, automotive, and household wipes, with complete production lines featuring hydroentanglement bonding.
New technologies
Saurer has implemented automation in yarn spinning, which includes an automatic conveyor transport system, a roving bobbin transport system, and the use of multilink or direct link technology. These advancements significantly minimize the need for physical interaction and enhance overall efficiency. Robo Textiles from Germany provides automatic loading/grippers for sewing machines, eliminating the need for a double handle, a crucial process for the precise separation and pick-up of textiles, a fundamental aspect of fabric processing.
3D knitting is a manufacturing method that uses computer-aided design (CAD) and control of knitting needles and threads to produce seamless and sustainable clothes. This enables to create complex and customizable textile structures with the reduction of material waste enhance the overall sustainability.
DyeRecycle, a spinout from Imperial College London, provides two innovative green chemistry technologies for the separation of dyes and textiles. DyeRecycle Synthetics and DyeRecycle Celullosics remove dyes from fibers, resulting in decoloured fiber that is clean and free of dye. This technology is ideal for mechanical and chemical fiber recyclers. It can be utilized as a dye bath for new fabrics or extracted and sold. DyeRecycle garments significantly reduce the use of chemicals, water, and carbon emissions. Alchemie and Imogo develops the spray dyeing and finishing reduce the drastic usage of water, energy, chemicals, and wastewater (up to 90 %), this will be promising for the future textile coloration industry.
Fabricon specializes in developing cutting-edge technology for spray-on fabric applications. Their innovative solution allows for the seamless creation of T-shirts sprayed directly onto the body, providing instant and effortless clothing options. Simplifiber is an advanced technology that transforms fibers into 3D shapes, such as the upper part of a shoe. This innovative approach significantly reduces the number of resources required compared with conventional manufacturing methods.
Aravin Periyasamy and Noora Raipale
VTT
For more information
Brochure-Textile-recycling_RZ update 11 06.indd (andritz.com)
Rieter Recycling Spinning System – Sustainability Solution
PDF Viewer (truetzschler-spinning.de)
Brochure-Textile-recycling_RZ update 11 06.indd (andritz.com)
Fabrican Spray-on fabric sprayable non-woven aerosol technology (fabricanltd.com)